The Future of Flight: Exploring 3D Printed Wings
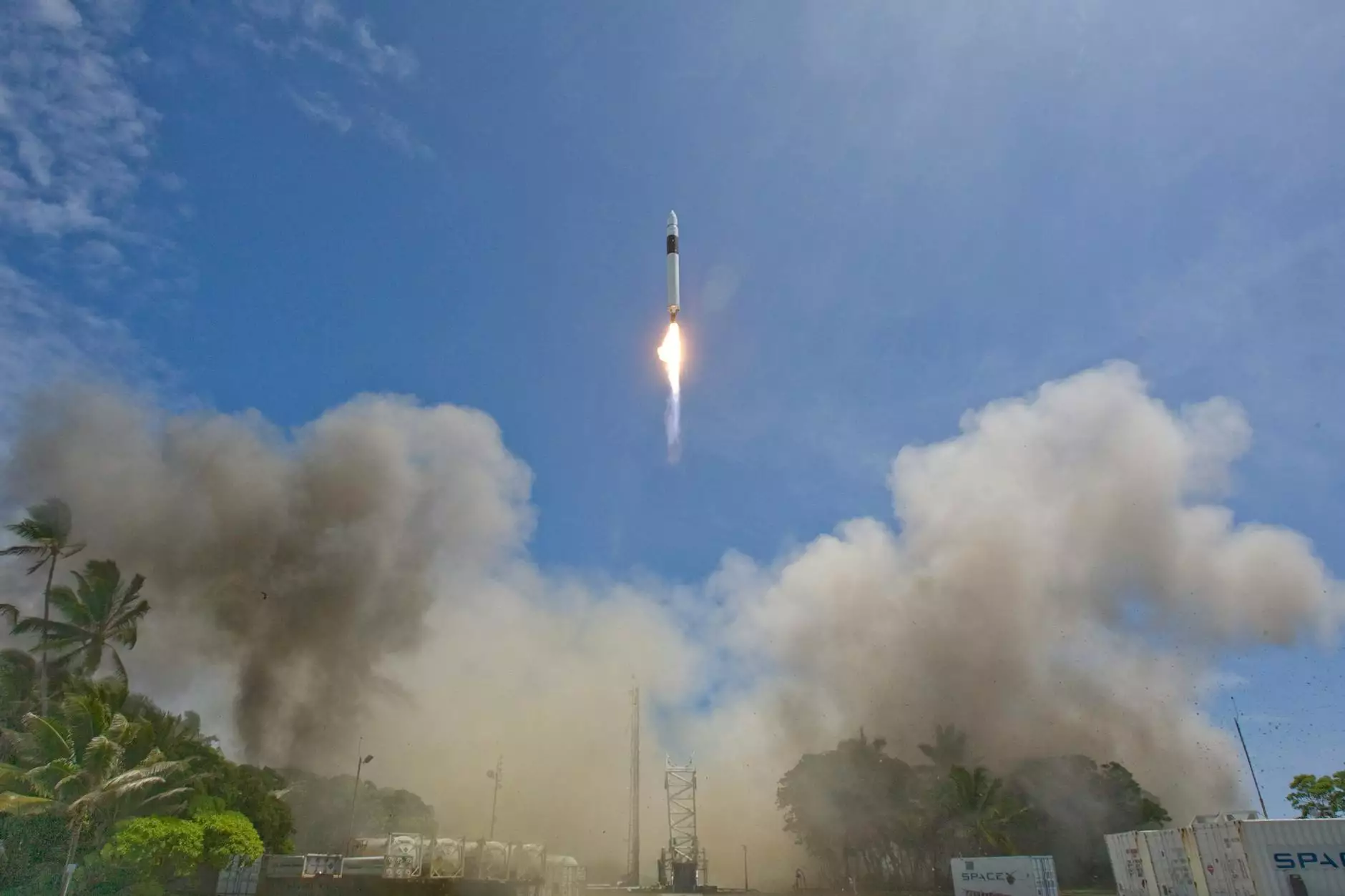
In an era defined by rapid technological advancements, the aviation industry stands at the forefront of innovation. One of the most exciting developments in this sector is the application of 3D printed wings. This cutting-edge technology not only promises to revolutionize the way we design and manufacture aircraft components but also sets the stage for greener, more efficient flying.
Understanding 3D Printing Technology
3D printing, also known as additive manufacturing, involves creating three-dimensional objects from a digital file. This process allows for the fabrication of complex shapes and designs that would be impossible or prohibitively expensive to produce using traditional manufacturing techniques.
The technology operates in several stages:
- Design: Using specialized software, engineers create a 3D model of the desired component.
- Slicing: The model is divided into horizontal layers, allowing the printer to build the object layer by layer.
- Printing: The printer deposits material according to the sliced pattern, slowly building the final product.
- Finishing: Post-processing techniques enhance the surface quality and mechanical properties of the printed wings.
The Importance of Wings in Aviation
Wings are crucial components of an aircraft, influencing its aerodynamics, stability, and overall performance. Traditional wing manufacturing methods often involve the use of heavy materials and complex assembly processes. However, with the advent of 3D printed wings, the industry is witnessing unprecedented changes.
Advantages of 3D Printed Wings
The benefits of using 3D printed wings in aviation are numerous:
- Weight Reduction: 3D printing allows for the creation of lightweight structures that maintain strength and durability, significantly reducing the overall weight of the aircraft.
- Design Flexibility: Engineers can experiment with complex geometries that improve aerodynamic efficiency and performance.
- Rapid Prototyping: Quick iterations and modifications can be made, reducing the time from concept to production.
- Material Efficiency: Additive manufacturing minimizes waste by using only the necessary amount of material for each part.
- Cost-Effectiveness: Over time, the reduction in material waste and labor costs can lead to significant savings in manufacturing expenses.
Current Applications of 3D Printed Wings
The integration of 3D printed wings is already gaining traction in several aviation projects worldwide:
Commercial Aviation
Major airlines and aircraft manufacturers are exploring 3D printing technology to create prototype components for their aircraft. This allows them to test innovative designs that could lead to performance enhancements in fuel efficiency and payload capacity.
Military Applications
The military is investing in 3D printed wings for unmanned aerial vehicles (UAVs). The ability to quickly produce parts enables rapid deployment and adaptation in response to changing mission requirements.
Personalized Aviation Solutions
As the industry moves toward personalized aircraft designs, 3D printed wings empower hobbyists and small manufacturers to create tailored solutions that meet specific needs without the constraints of traditional manufacturing.
The Environmental Impact of 3D Printed Wings
Reducing the carbon footprint of aviation is a critical goal in combating climate change. 3D printing contributes to this initiative in several ways:
- Sustainable Materials: Innovative materials like bio-composites and recycled plastics can be used in 3D printing, leading to a more sustainable manufacturing process.
- Energy Efficiency: The lightweight designs of 3D printed wings enhance fuel efficiency, reducing emissions per flight.
- Localized Production: 3D printing can be done closer to the point of use, cutting transportation emissions and costs.
The Future of 3D Printed Wings
The future of 3D printed wings looks promising as research and development continue to advance. Anticipated trends include:
Regulatory Developments
As 3D printing technology becomes more common in aviation, regulatory bodies will establish guidelines to ensure safety and quality. This will pave the way for broader acceptance and integration into mainstream aviation.
Increased Material Innovation
Research into new materials designed for 3D printing will lead to lighter, stronger, and more durable components. Such innovations will further enhance the performance and safety of 3D printed wings.
Collaborative Design Efforts
Collaboration between engineers, designers, and industry experts will foster innovative approaches to wing design, making full use of the capabilities of 3D printing. This cross-disciplinary effort will lead to the creation of highly efficient and effective wing designs.
Challenges and Considerations
While the potential for 3D printed wings is significant, several challenges must be addressed:
- Technical Limitations: Current 3D printing technologies are still evolving, and scaling up production for large components presents challenges.
- Quality Assurance: Ensuring that each component meets the rigorous safety standards required in aviation is crucial.
- Cost of Materials: High-performance materials used in printing can be expensive, particularly for small-scale manufacturers.
Conclusion
The revolution of aviation technology through 3D printed wings has the potential to transform how we approach aircraft design and production. As the aviation industry continues to embrace this innovative technology, we can expect improvements in efficiency, sustainability, and performance. The journey towards a future of lightweight, efficient, and environmentally friendly flying has just begun, and the possibilities are endless.
As more stakeholders invest in this technology, the concept of mass-customized aircraft could soon become a reality, highlighting the vital role of 3D printed wings in the aviation landscape.
For more information on the advancements in 3D printing technology and its applications in aviation, visit 3DPrintWig.com.